
I’ve been involved in three events recently, each having a focus on reducing the carbon footprint created by the construction industry:
- The RMIT University PCPM Industry and Research Awards Night 2023, where I presented the CIOB Certificate of Excellence to a student CIOB member in their final year with the highest GPA in Construction Management. A significant proportion of the student projects on show at this event had a focus on sustainability and carbon reduction.
- ZERO is an industry group focused on embodied emissions from construction. Our latest discussion was on tools to measure embedded carbon in buildings. For more on Zero see: https://zeroconstruct.com/
- Representing the Chartered Institute of Building (CIOB)[1] at the Chartered Institute of Building Services Engineers (CIBSE) awards night for young engineers where the focus was again on reducing carbon from construction activities, with at least some of the award winners looking at the full lifecycle of a building.
Given construction activity accounts for 12% of all human carbon emissions, reducing the industries emissions makes sense. But to be effective, this needs a wholistic view of the carbon lifecycle in the built environment.
At the moment, the trend seems to be focused on measuring the carbon embedded in a structure during the building process. The tools discussed in the recent ZERO Zoom meeting need improving, but they are designed to plug into a BIM model[2] and calculate the embedded carbon.
While this is useful, and the technology is exciting, I have a feeling this focus is missing 90% of the problem. Just focusing on ‘the building’ creates the impression low carbon buildings are relatively expensive and designing for minimum carbon in the structure can cause overall emissions to rise significantly. This is a lose-lose outcome.
From my perspective, some of the easiest ways to reduce carbon overall and reduce building costs lay in other areas. The cost of a building through its life is expressed by the ratio 1:5:200 where:
– 1 is the cost of construction
– 5 is the cost of facilities maintenance and refurbishment through
the life of the structure
– 200 is the cost of the operations undertaken within the structure.
While this is a financial ratio, spending money involves doing work which generally creates carbon, probably in similar proportions. Therefore, a small saving in construction that causes an increase in the ownership/operating costs is going to be highly counterproductive.
A few random ideas on ways to reduce carbon within a whole of life perspective include:
Passive Design to reduce operating/ownership costs. One example is eaves on domestic houses.
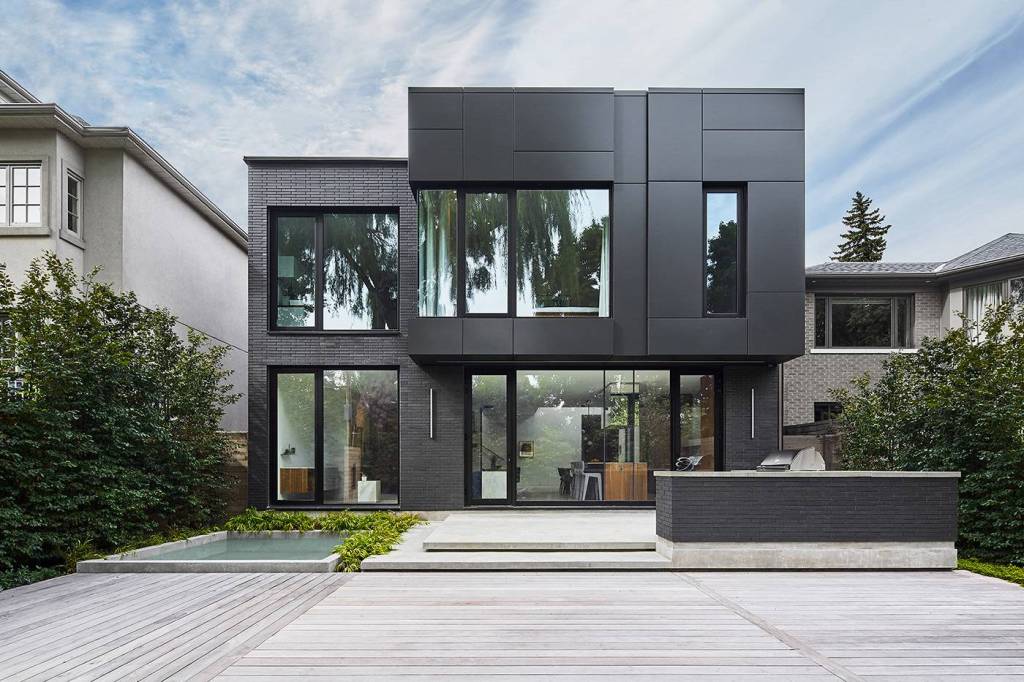
Traditional houses had relatively wide eaves (particularly in warmer climates such as most of Australia). These provided shading to the walls and windows. Modern design eschews eaves, which means the walls and windows are hit with the full blast of summer sun. The cost of the extra air-conditioning over the next 50+ years will far outweigh the cost of the eaves. Add in the colour – dark colour absorb heat, the house pictured may be a good design for the northern half of Sweeden, but it is not very carbon friendly in Sydney. Other design considerations include natural lighting, passive ventilation, etc.
Design for a long life a well-constructed house or other building should have a life of 100+ years. The way the structure is used will change but if the basic frame is designed for a long life, it can be reused and redefined for far less cost than demolishing it and building something else. One really daft trend has been to clad buildings with timber (driven by various ‘star-rating’ schemes). Timber rates very well if you focus just on the carbon embedded during building. It is a disaster if you allow for repainting many times, then ripping off the rotting façade in 20 to 30 years’ time, sending the decomposing timbers to a tip and replacing the cladding with something else. A brick wall may be more carbon-intensive than a wood wall, but a well-built brick wall will still be standing and doing its job in 200 years’ time.
Design to reduce construction waste every skip load of rubbish shipped off site is wasted carbon (and money). There are many ways to reduce construction waste including: modularisation, off-site manufacture, intelligent packaging, etc. This is probably the easiest of the ‘low hanging fruit’ – saving costs and reducing carbon at the same time. Unfortunately at the moment, the tools used to measure embedded carbon don’t really have any way to measure the carbon in waste.
Design for maintenance and repurposing rather than demolition. Making building maintenance and repurposing easy, should increase the value of the structure while reducing its overall carbon footprint. But achieving this also needs a change in mindset from building owners. The Victorian government has announced the replacement of 100s of social housing units. There is no argument they are old and do need replacing. However, their default approach is to demolish everything and re-build from scratch. But the buildings have solid concrete frames with another 100+ years of life – a carbon sensible approach would be to strip the frames and design new cladding, interiors, and services. Done well this would be a lower cost and lower carbon option.
Conclusion
The need to reduce the carbon footprint of the built environment is a given, and new materials and improved measuring tools are both important. But, just focusing on one aspect, the carbon embedded in the construction process is a recipe for failure. The important missing elements are:
- Changing thinking and attitudes of asset owners. Governments are responsible for a very large percentage of the overall built environment and their innate conservatism is creating thousands of tones of carbon: Local Authorities are largely ignoring recycled and low carbon alternatives for road surfacing. The Victorina Government immediately defaults to ‘knock everything down and rebuild’ in its social housing renewal. Etc.
- As with other aspects of construction, remember the 1:5:200 ratio. Building cheap / low carbon is only good if you have no interest in the operation and maintenance of the facility. Nirvana is building cheap / low carbon structures that are easy to maintain, efficient to operate, and have a long life.
- Requiring a whole-of-life approach to carbon in the built environment. This should be through amendments to building regulations and to measurement systems. Think of the impact if developers had to provide certified information on the 10-year and 20-year cost of ownership to prospective buyers…….
The emerging tools and technologies are important tools in the process of reducing the carbon footprint of the construction industry, but real change needs a wider focus. And as per the title of this post, in the construction industry, the wider built environment, and every other aspect of commercial, professional, and personal life, every decision you make, every action you take leaves a carbon footprint – it needs to be included in your thinking.
See also:
‘Built to Last‘ for a discussion on sustainability: https://mosaicprojects.wordpress.com/2023/07/22/built-to-last/ and
‘Shining the light towards low-carbon construction‘: https://mosaicprojects.wordpress.com/2023/02/27/shining-the-light-towards-low-carbon-construction/
For more on carbon in the construction industry see: https://mosaicprojects.com.au/PMKI-TPI-005.php#GB
[1] The CIOB were early proponents for the reduction of carbon in the construction industry and a lot of the thought above are founded on my involvement with the CIOB Carbon Action 2050 campaign unfortunately this initiative seems to have faded in the last decade: https://www.ciob.org/industry/politics-government/campaigns/carbon-action
[2] For more on BIM Modelling see: https://mosaicprojects.com.au/PMKI-ITC-011.php#BIM